Client Success Story
How Sealy Mattress Company of New Jersey Modernized Operations to Usher in a New Era of Growth and Productivity
Industry: <Industry here>
Solution: <Industry here>

background
Introduction
A fourth-generation, family-owned business, Sealy Mattress Company of New Jersey (Sealy NJ) manufactures Sealy and Stearns & Foster sleep products in Paterson, New Jersey. Sealy NJ is the only domestic licensee of Sealy and Stearns & Foster and works closely with its licensor, Tempur Sealy International (TSI), to service mattress retailers across its territory in the Northeast United States. While Sealy NJ operates a productive manufacturing facility built on 99 years of mattress manufacturing acumen, the company faced a daunting challenge: modernizing outdated systems and processes that prevented it from reaching its full potential.

Challenge
Outdated, unsupported technology:
Sealy NJ relied on a 25-year-old green-screen ERP system that it shared with TSI. This system was cumbersome, difficult for Sealy NJ to customize, and added risk to the business because it was difficult and expensive to maintain.
Limited visibility:
Sealy NJ also needed more visibility to measure and improve production capacity and efficiency. Without quantifiable metrics or modern KPIs, Sealy NJ couldn’t effectively track product quality, material waste, worker downtime, labor hours per piece, or cost to poor quality. A lack of visibility is common in manufacturing. According to one report, 40% of manufacturers have no visibility into the real-time status of their company’s manufacturing process.
Manual, inefficient processes:
Sealy NJ operated how it had for decades, relying on paper-driven processes vulnerable to errors and manipulation. For example, the workers’ incentive earnings process involved scanning chit tickets, printing reports, and then manually entering data and calculating pay in Excel. Sealy NJ was not alone in this problem, as Forbes reported that 95% of manufacturers still use paper-based processes for some or most of their activities.
Project Goals
- update unsupported software
- increase visibility into real-time data
- replace manual paper-driven processes
“MCA Connect drives remarkable transformations with global clients. They make supply chain dreams a reality with the Microsoft Cloud, cutting on-hand inventory while maximizing fill rate performance, eliminating digital debt, enabling end-to-end visibility, and unlocking total global flexibility.”
Solution
Sealy NJ’s ERP system challenges presented a risk to the business that ownership could no longer tolerate. Sealy NJ recognized the need to modernize its systems and processes and usher in a new era of operational excellence. They sought to achieve this with the support of a modern ERP solution and the improved functionality, efficiencies, and insights it could provide.
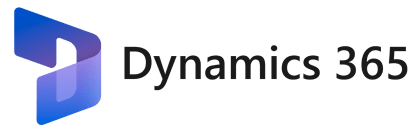
With support and guidance from TSI, Sealy NJ decided to implement Dynamics 365 Finance and Supply Chain Management.
Sealy NJ evaluated and considered several partners for this project. In the end, MCA Connect’s® deep manufacturing expertise set us apart. This expertise became evident when we toured Sealy NJ’s facility and asked insightful questions to understand their business, challenges, and goals. According to a report by Deloitte, manufacturing expertise is one of the most critical factors for successful digital transformation.
Results
By implementing Dynamics 365 with MCA Connect’s deep manufacturing expertise and strategic implementation methodology, Sealy NJ was able to:
Outdated, unsupported technology:
Sealy NJ relied on a 25-year-old green-screen ERP system that it shared with TSI. This system was cumbersome, difficult for Sealy NJ to customize, and added risk to the business because it was difficult and expensive to maintain.
Limited visibility:
Sealy NJ also needed more visibility to measure and improve production capacity and efficiency. Without quantifiable metrics or modern KPIs, Sealy NJ couldn’t effectively track product quality, material waste, worker downtime, labor hours per piece, or cost to poor quality. A lack of visibility is common in manufacturing. According to one report, 40% of manufacturers have no visibility into the real-time status of their company’s manufacturing process.
Manual, inefficient processes:
Sealy NJ operated how it had for decades, relying on paper-driven processes vulnerable to errors and manipulation. For example, the workers’ incentive earnings process involved scanning chit tickets, printing reports, and then manually entering data and calculating pay in Excel. Sealy NJ was not alone in this problem, as Forbes reported that 95% of manufacturers still use paper-based processes for some or most of their activities.
“MCA Connect drives remarkable transformations with global clients. They make supply chain dreams a reality with the Microsoft Cloud, cutting on-hand inventory while maximizing fill rate performance, eliminating digital debt, enabling end-to-end visibility, and unlocking total global flexibility.”
What’s Next?
Over time, Sealy NJ aims to reduce costs, improve efficiency, and expand capacity by automating and streamlining production. Sealy NJ also seeks to improve the quality of its products by introducing additional quality control points (leveraging Dynamics 365’s Nonconformance feature that was customized as part of the project). They’ll then use the accumulated data to improve inspection sampling plans and other quality processes to better hold production operators accountable for their work.

About MCA
Through passion and deep industry expertise, MCA Connect® helps manufacturers succeed by unlocking innovation with actionable business insights. Our strategic solution and industry intelligence help manufacturers gain visibility, improve profitability, and achieve a competitive edge. Contact us today to learn how we can help solve your biggest manufacturing challenges.
Explore and Learn
Explore More Resources
We know manufacturing because we’ve spent over 20 years in the industry, solving problems and uncovering new opportunities with Microsoft. Explore our resources to gain insights from our industry experts on trends, challenges, and opportunities, so you can better serve your customers.

Lorem Ipsum News Announcement Dolor Amet
How manufacturers use Power Platform to automate shop floor processes and become an intelligent factory.

Lorem Ipsum News Announcement Dolor Amet
How manufacturers use Power Platform to automate shop floor processes and become an intelligent factory.

Lorem Ipsum News Announcement Dolor Amet
How manufacturers use Power Platform to automate shop floor processes and become an intelligent factory.

Lorem Ipsum News Announcement Dolor Amet
Duis aute irure dolor in reprehenderit in voluptate velit esse cillum dolore eu fugiat nulla pariatur.